Exampe of Summary How Technology Speeds Up Time and How Its Slowing Down Again
We have already explained what is speed loss and how to mensurate information technology. In this article, we have a closer look at how manufacturers reduce speed loss to increase their production effectiveness. Where possible, we illustrate different types of speed loss with specific examples, which we take from the experience of our clients and a few recent inquiry papers.
In this commodity, we would similar to note that we focus on how to solve product speed problems without buying new or ameliorate equipment.
The Tradeoff
One more note, before we dive into the topic. Often there is a tradeoff between the three OEE components: performance (production speed), availability (duration of stops), and quality (rejects).
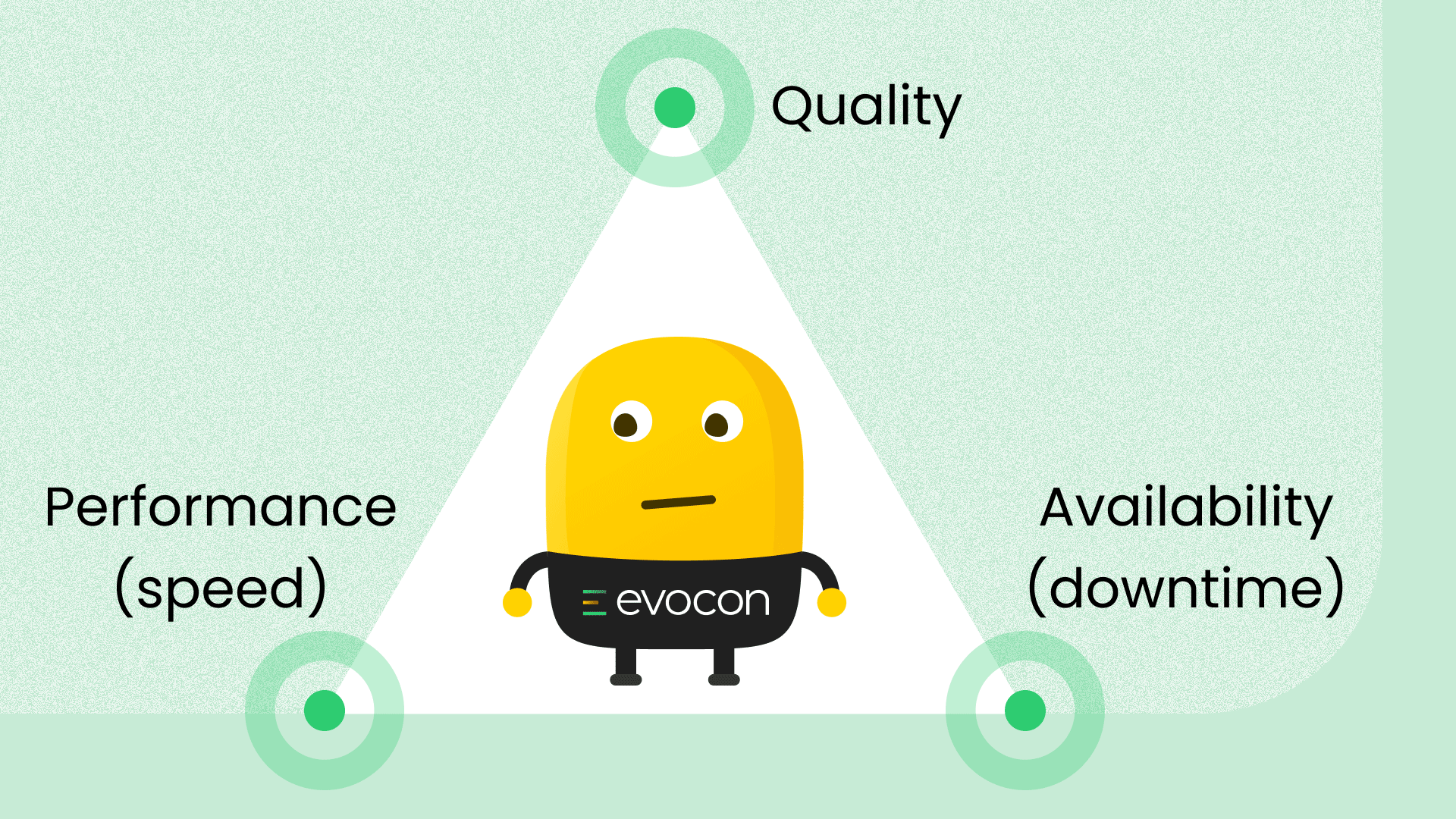
Increasing the speed also much can result in additional downtime and reduced quality. For example, running a machine too fast may cause higher levels of vibration, this tin affect the quality and may upshot in rejected products. It can also speed up the wearing of the equipment, resulting in repairs, extra cost for spare parts, and shortened lifespan of the machine.
Then, let'due south remember that while we are discussing the trouble of slow speed and micro stops, we need to keep in listen how it affects availability and quality.
Only let's dive in now. Nosotros hash out three types of speed loss problems:
- Human related
- Production related
- Technology related
Human factors
Optimal process
For production lines with a high degree of manual work, the biggest potential lies in organizing the process to brand the manual piece of work easier, faster, and more motivating. You may consider:
- The steps of the process. Perhaps it is possible to skip some steps or combine two tasks into one. In certain cases, it is useful to rearrange the order of the steps to create a more balanced flow, avoiding bottlenecks or waiting. Or, peradventure some tasks could be performed on several products at a time, instead of one.
- The right people in the correct places. People perform differently at different tasks. Consider switching people around in the areas of problematic performance.
- The correct tools. Check if the right tools are bachelor and if they are working properly or malfunctioning all the time. Perchance there is a possibility of getting better tools, such as electric tools instead of transmission ones.
- Clean and tidy workspace. It is easier to move around and find tools and materials in a tidy environment. There is a psychological effect also: information technology affects motivation.
- Pattern of tasks to be physically comfortable. When people are comfortable at work, they perform much faster. This is the area of ergonomics, a whole science with plenty of inquiry material bachelor.
Ergonomics
Ergonomics takes into business relationship human posture, motility, residual, the field of vision, and strength required to practice the tasks.
1 instance of awarding of ergonomics is a Japanese factory that started to make protective gowns. A worker noted that it is difficult to bend frontwards to reach for the edge of the fabric when folding it. She suggested that having two people to fold the sheets would brand the task faster and easier, increasing the efficiency even when double the labor price is taken into account.
As a result, the company was able to increase speed significantly. Sentry the video for this and other corking examples of increasing production efficiency:
The learning curve
The learning curve, also called the experience curve, basically means that experienced staff performs faster. While feel automatically increases with hours spent at performing the chore, at that place are as well ways to assist it:
- Increasing specialization. People piece of work faster when they perform the aforementioned task all the time. Still, be careful not to specialize too much. The downside of this is a lack of motivation and inflexibility.
- Decreasing turnover. One great example of this is ane of our clients, who created a bonus system effectually OEE to motivate workers.
- Standardizing procedures. Ensure that procedures are standardized and instructions are bachelor to everyone so that people don't experiment likewise much or autumn into "bad habits". Nevertheless, don't forget to welcome discussions or new ideas.
- Sharing best practices. Report how the best performers operate and encourage others to copy. Then, standardize practices that work universally.
Notation: Evocon's system has built-in functionality that enables recording and sharing best practices.
Allow'southward illustrate this last point using an example from one of Evocon'south clients, a metallic component producer Meconet.
Meconet, had a "raw textile filling" upshot come up up at the top of their reanimation reasons' list. Looking at the data, they saw that some operators filled the raw cloth feeder much faster than the others. A visit to the store floor revealed that more than experienced operators prepared material earlier machines ran out of it. Then, the fastest operators were asked to share their manner with the balance. This simple solution reduced the boilerplate filling fourth dimension by 30%.
In this last instance, the manufacturing plant solved an availability issue, not a speed loss issue. Notwithstanding, with Evocon, both downtime and speed loss issues are recorded, also as the reasons why those problems are occurring. This lets our clients bargain with speed loss as effectively as with downtime.
Learn more than: Meconet: fifty% Increase in Operating Time in v Months
Depression speed targets
Another homo-related issue we encounter very often is when speed targets are set too low. The practiced news is that the solution is simple – to increase the target by adjusting ideal cycle time or maximum speed in your OEE software settings to be a realistic, but a more challenging number.
We have a guide on how to do this, even if your supplier hasn't provided your machines' official maximum speed. In summary, it works like this: detect out what is the processes' operation when it runs at information technology's best, prepare information technology as the initial goal, and communicate to the personnel. One time this speed target is achieved with ease, run into if you tin can increase the target once more.
Product scheduling
One interesting source of production line efficiency is the psychological effect of production scheduling. To illustrate this, we utilise a example study from the inquiry newspaper "Why tedious downward? Factors affecting speed loss in procedure manufacturing", which analyzes a edifice insulation manufactory in Europe.
The factory makes several different products using two production lines. Each product has a unlike speed target.
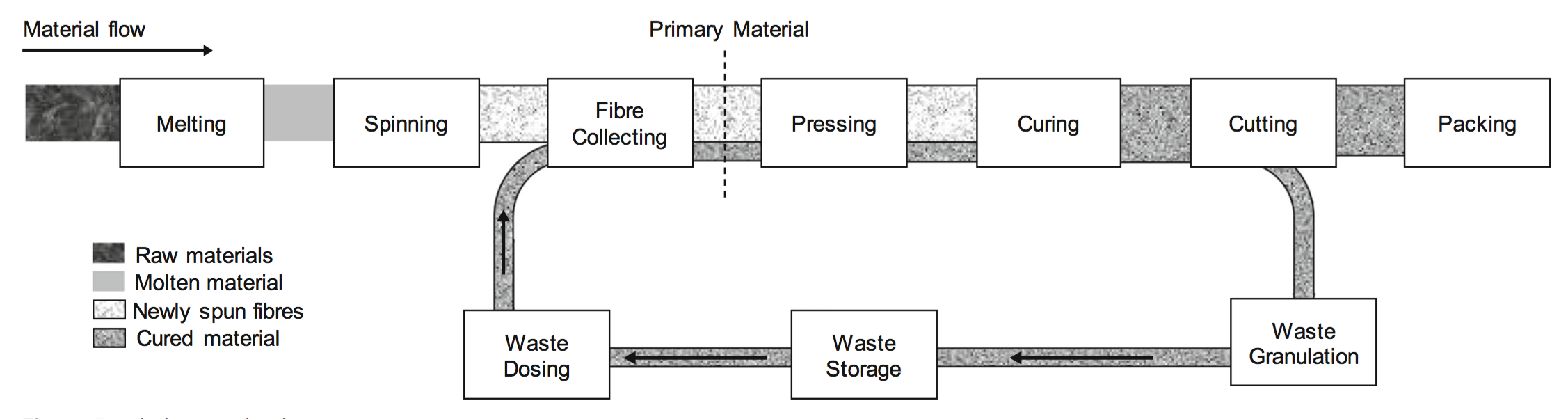
The factory collected detailed information for 3 months. Here is what they establish subsequently analysis.
- The psychological outcome of unlike speed product schedule. Researchers noticed that the scheduling of product batches had an interesting upshot on operators' perception of speed targets. Whenever operators knew that their next production had a loftier speed target, they tended to increase the electric current product'south speed in preparation for the faster product. That style, if products with the most speed loss were scheduled just before products with high speed target, production became faster, resulting in lower speed loss for the whole product mix. Similarly, it took operators a while to "wind-down" later on running a fast product. Then, a product with high speed loss could be scheduled non simply before a fast production but also afterward it.
- The length of run time. Another variable that was associated with decreased speed loss was the length of run time. The researchers had expected that longer run times would result in less speed loss. However, that was only true for run times that were longer than two hours. The analysis showed that for run times shorter than two hours, the relationship reversed: shorter run times resulted in less speed loss.
These ii examples bear witness that an in-depth assay of production scheduling and its impact on speed can offer cost-effective solutions to reduce speed loss.
Product Factors
Product changeovers
While changeovers cause downtime and not speed loss, speed also decreases because frequent changes destabilize process settings. Therefore, information technology is important to analyze if information technology is possible to produce larger batches instead of smaller ones.
Product quality
Product quality of finished goods can cause modest stops equally the line has to exist stopped to ready quality problems. For example, if boxes are non closed properly on a packaging line, an operator has to make small-scale stops to close them. In a case like this, the solution could be either to deadening the line down just enough to avoid quality problems or to investigate whether quality could be maintained without slowing downwardly the process.
Also, consider if the quality of your products is besides good. The product's quality needs to exist exactly every bit specified or a trivial scrap ameliorate, but information technology does not need to be much improve. For instance, a metal function may not demand a fine surface end if it is going to exist used somewhere where it doesn't matter. So, you lot might speed up the procedure past accepting a college level of roughness.
Material quality
The quality of fabric may boring down production lines. For example, a product is assembled from a few parts glued together. When a lower quality glue is used, the parts don't stick together equally well as ordinarily. And then, the line is run slower to give the glue time to practice its chore. In this case, measuring this speed loss helps to make up one's mind whether it is worth purchasing ameliorate quality glue.
Engineering science Factors
Equipment design weakness
Sometimes car producers are non the best specialists of the production process, or perchance your production process is unique, and the automobile does not fit the process ideally. You need to question existing solutions: are they the best for your environment and your processes? Maybe, small add together-ons or changes to the motorcar could help increment the speed. Let'south look at an instance of this problem and its solution.
For this example, we apply a instance written report of a steel establish in India from this research paper: "Kobetsu Kaizen Losses Analysis to Raise the Overall Plant Effectiveness in Steel Manufacturing Industry."
Example of an equipment design weakness
The information collected from May 2017 to July 2017 showed that out of 16 TPM losses, pocket-sized stops caused the biggest loss in monetary terms. This contributed to the fact that the performance rate was but 72%, the lowest of the iii OEE components (availability, performance, and quality).
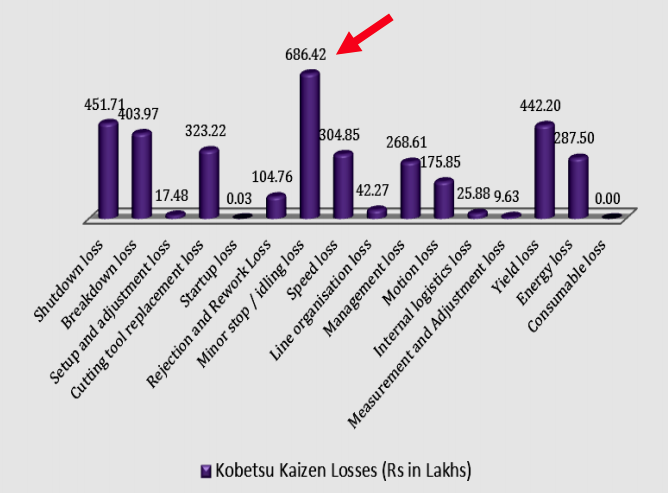
Researchers used five Whys assay to discover the root cause of the problem:
- Why is small-scale stoppage/idling loss so loftier? Due to frequent jamming of belch chutes used to slide material from a conveyor belt to a lower level.
- Why does frequent jamming occur? Due to malfunctioning of the discharge chute.
- Why does belch chute malfunction? Due to a heavy period of fabric from it.
- Why is there a heavy menstruation of fabric from it? Due to no command at the inlet of the chute to control the incoming textile flow.
- Why is there no command at the inlet of the chute?
ACTION: Cosmetic action recommended as Kaizen to establish constructive control to forestall such type of failure.
RECOMMENDATION: A periodic hammering arrangement needs to be established at the outlet to prevent blockage of material.
Later on implementing the solution, the performance rate increased from 72% to 87%, which saved the steel plant about Rs 530 lakhs ($941,000) per month.
Tip: From our experience, many of our clients experience minor stops that they were not aware of previously. By implementing an automated organisation to rail production, yous get the transparency yous demand to know if this is a waste that affects you or not.
Limits to the speed of physical processes
Whenever you work on increasing the speed of the physical handling of materials, you demand to bargain with four main constraints that limit your efforts. These are:
- Machine stiffness
- The ability of tools to advance
- Heat transfer
- Fluid menses
We will briefly review each of these constraints to the speed you can achieve and what are the options to increase the speed without ownership new equipment. This chapter is based on the enquiry paper "Manufacturing at double the speed" (Journal of Materials Processing Technology, March 2016).
ane. Machine stiffness
If you have ever driven a sports machine, y'all may have noticed how "potent" it is to sit down in. This is considering sports cars are designed for high speed. The aforementioned rule applies to machines in your factory.
As you run your machines faster, at some indicate, you lot get vibration and chatter. The stiffer your machines and materials are, the faster you tin can run them earlier this happens.
Here is an example from Principles of Mod Grinding Technology:
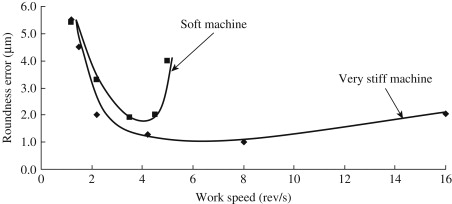
To increment stiffness in your production without new equipment, y'all could utilise stiffer materials that you are working with. Some other option is to reduce the size of those materials and increase their weight. Generally, smaller and heavier things vibrate less.
As for machines themselves, let's recall that machines are screwed into the flooring to proceed vibration depression. Sometimes information technology is possible to practice something in this fashion when adjusting the machine to a specific situation or product. Basically, you can reduce the movement of the parts of your machine by "fixing" them in identify when you lot don't need full motion. In other words, if yous don't need all the flexibility that the machine offers, y'all can reduce it to achieve better stiffness.
2. Dispatch of tools
If you lot accept a CNC machine, or robotic artillery that move parts from one place to another, or cranes that elevator and move heavy objects, the speed of this procedure depends on how fast these machines, artillery, and cranes can move.
The tools move along a path, where they demand to speed upwardly, irksome downwardly, change direction. How fast this motion can happen depends on how fast these tools can accelerate.
Yous tin ameliorate dispatch with a good motility control organization. A good organisation can create a smoother and faster movement while avoiding jerking motions.
Also, look at the path of the move itself. Does it have to be as complex equally it is? Can you achieve the same result with fewer movements? Is it possible to rearrange the path to shorten the distance?
3. Heat transfer
An everyday example of a heat transfer problem is a chicken that you are trying to bake in the oven and ensure that it is well cooked within but not burned exterior. You would accept to limit the cooking speed to let the heat to reach the inside of the chicken.
The same challenge exists in manufacturing when you need to rut the eye of a workpiece as fast as possible without melting or transforming the surface of this workpiece.
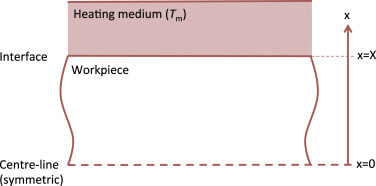
What are the options to increase the speed in this example?
Mostly, the speed of this process depends on the size and thermal electrical conductivity of the part:
- Doubling conductivity at the signal of deport halves the time required for heating.
- Halving the thickness of the workpiece also halves the time required for heating.
4. Fluid flow
When cutting, grinding, or otherwise forming parts, you oft need to utilize fluids for lubrication or to avoid overheating. These fluids ordinarily reach the required location through a tube.
Hither are the options yous have:
- To use a thicker tube through which the fluid travels. This is the well-nigh effective solution, but it may require higher pressure.
- You lot could besides shorten the tube or brand sure there are no sharp bends in it. This helps, although it is usually less effective than a thicker tube.
- You could reduce the viscosity of the fluid. You could employ a different, less viscous fluid, but fluids also alter their viscosity when their temperature changes, and so y'all could take advantage of that also.
- And finally, it might be possible to submerge the entire procedure in the fluid, for example, when grinding a function, that way completely avoiding the need to deliver the fluid.
Interestingly, one of our clients had a speed loss outcome related to the viscosity of the fluids, only in this example, it was the viscosity of the product itself. Information technology was a juice manufacturer, and the juice on the bottling line was splashing besides much in warm temperatures, resulting in the tiresome down of the line during summertime. Nevertheless, this is more of an environmental limitation rather than a technological one.
Ecology limitations
The last category of technology-related issues is environmental limitations.
One example of that nosotros have just given above, concerning the manufacturer of juice. Another instance would exist fertilizers, where chemicals are sensitive to the temperature of the environment.
A dissimilar blazon of environmental limitations stems from regulations, such every bit limits on emissions.
Conclusion
Permit'south sum upwards the types of speed loss problems discussed in this article and how to address them.
Human related
- Address process steps, rotate people, provide tools, tidy upward the workspace
- Design tasks to exist physically comfortable
- Speed up the learning curve
- Increase speed targets
- Find the optimal production schedule
Product related
- Reduce changeovers
- Find the right level of quality
- Use materials of improve quality
Engineering related
- Improve equipment design
- Increase machine stiffness
- Improve dispatch of tools or reduce the need to accelerate
- Speed up heat transfer
- Increase fluid menstruum
- Take into business relationship the sensitivity of materials to the temperature
- Accept into account the environmental regulations
Sources
- "Why slow down? Factors affecting speed loss in procedure manufacturing" Trattner, A., Hvam, L. & Haug, A.
- "Kobetsu Kaizen Losses Analysis to Heighten the Overall Plant Effectiveness in Steel Manufacturing Industry" Dr. Manish Raj, Shubham Swaroop, Saureng Kumar, Raj Bhushan, Vikalp Kumar, Grand G Borkar
- "Manufacturing at double the speed" Julian M. Allwood, Tom H.C. Childs, Adam T. Clare, Anjali K.Thou. De Silva, Vimal Dhokia, Ian M. Hutchings, Richard Thou. Leach, David R. Leal-Ayala, Stewart Lowth, Candice East. Majewski, Adelaide Marzano, Jorn Mehnen, Aydin Nassehi, Erdem Ozturk, Mark H. Raffles, Raj Roy, Islam Shyha, Sam Turner
Source: https://evocon.com/articles/examples-of-speed-loss-in-manufacturing/
0 Response to "Exampe of Summary How Technology Speeds Up Time and How Its Slowing Down Again"
Post a Comment